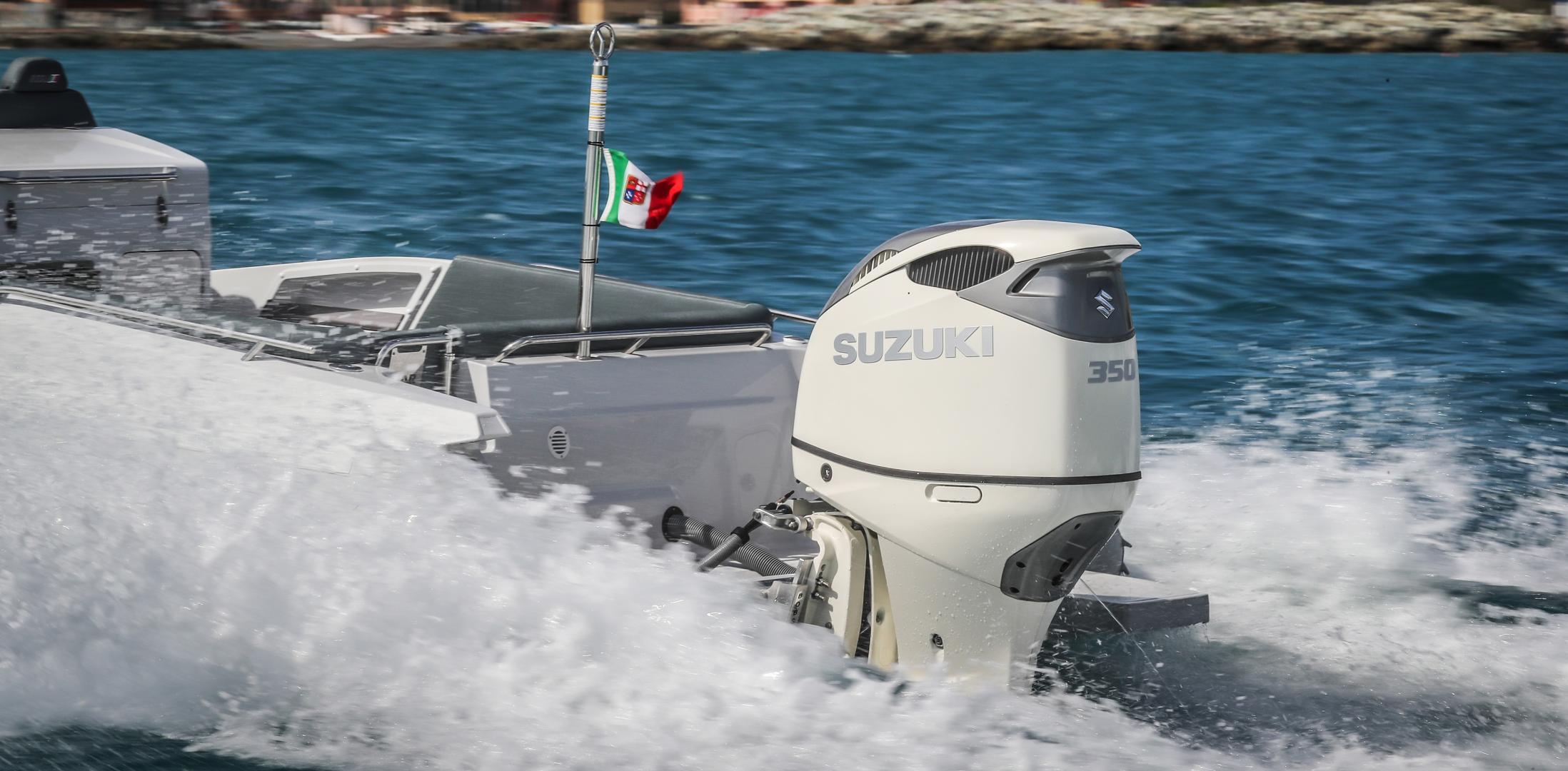
ZAR 85SL, Suzuki DF350A
La propulsione della barca: l’equilibratura dei motori a scoppio
Se si trasforma l’energia meccanica in calore, un cavallo-ora equivale a circa 630 chilocalorie, che è il calore ottenuto bruciando 63 grammi circa di benzina. Ma se con la benzina alimentiamo un motore a scoppio, per ottenere un cavallo-ora ne occorrono circa 200 grammi, con un rendimento quindi bassissimo. Occorre allora chiedersi dove va a finire tutta l’energia che alimentiamo al motore ma che non ritroviamo come potenza motrice.
Il grosso se ne va con i gas di scarico e con il raffreddamento, ma ci sono anche il rumore, gli attriti e le vibrazioni o gli scuotimenti: per quanto possa sembrare strano sono tutte forme di energia dispersa che si tenta di minimizzare, oltre che per il confort, per diminuire i consumi e quindi migliorare l’efficienza del motore.
Quello di cui vogliamo parlare in questo intervento è legato alle vibrazioni ed agli scuotimenti, dovuti essenzialmente alle forze di inerzia che agiscono sul blocco motore.
Quello che i tecnici definiscono pomposamente “manovellismo di spinta rotativo” è una serie di meccanismi semplici che consente di trasformare il moto alternativo dei pistoni nei cilindri in moto rotatorio dell’albero motore. Se consideriamo infatti il più semplice dei motori, un monocilindrico, vediamo che essenzialmente è costituito da un cilindro entro il quale va su e giù un pistone, che con una biella è collegato alla manovella dell’albero motore.
Ad ogni giro dell’albero motore, (a parte le fasi utili di compressione, scoppio, espansione ecc., che per il momento tralasciamo), corrisponde un giro della manovella, e una salita ed una discesa del pistone.
Ad ognuno dei movimenti è associata una accelerazione, che produce una variazione di velocità e quindi una forza di inerzia, forza che tenta di opporsi appunto alle accelerazioni o alle decelerazioni. Ma quali sono queste variazioni di velocità? Sono essenzialmente tre: una relativa alla manovella; e le altre due al pistone.
La manovella.
Ad ogni moto rotatorio è associata una inerzia che tenderebbe a far partire per la tangente il corpo che gira: c’è quindi una accelerazione (che si chiama centripeta, cioè diretta verso l’asse di rotazione) che trattiene il corpo (nel nostro caso la manovella) sulla traiettoria circolare, ma che provoca uno scuotimento circolare del blocco motore, una centrifugazione che può essere molto pericolosa per le elevate frequenze che sono in gioco: a soli 3000 giri minuto la manovella compie 50 giri al secondo. Immaginate cosa succederebbe nel motore pensando al rumore ed agli scuotimenti della vostra lavatrice nella centrifugazione quando nel cestello c’è un malloppo di biancheria concentrato in un solo posto.
Per fortuna però questa vibrazione è eliminabile. Come? Mettendo sull’albero motore dei contrappesi equivalenti alla massa eccentrica rotante (manovella+testa di biella) e ad essa diametralmente opposti. Così la rotazione, veloce che sia, è perfettamente bilanciata ed in teoria non sono possibili vibrazioni. Aumenta però il peso dell’albero motore, e sappiamo che tutte le aggiunte di peso non sono certo utili a contenere il peso totale del motore. Sarà inoltre bene ricordare che i contrappesi sono necessari nei motori ad uno, due, e tre cilindri in linea; mentre da quattro cilindri, sempre in linea, è possibile evitare i contrappesi perché le manovelle a 180° si bilanciano a due a due simmetricamente rispetto al baricentro del motore. Questa simmetria è necessaria per evitare che uno scuotimento circolare semplice del baricentro (come nel caso di un solo cilindro) si trasformi in una oscillazione conica con il vertice nel baricentro, dovuta al fatto che le due manovelle generano una coppia attiva rotante che scuote tutto in giro la incastellatura del motore
Il pistone e l’occhio di biella
Ad ogni giro la velocità del pistone subisce due accelerazioni e due decelerazioni: accelera dal punto morto superiore, dove la sua velocità è zero, fino a mezza corsa, dove la sua velocità è massima: comincia a decelerare fino a velocità zero nel punto morto inferiore e poi accelera di nuovo fino a mezza corsa per poi decelerare tornando a fermarsi al punto morto superiore. Per un motore che gira a tremila giri al minuto (50 giri al secondo) significa che in un cinquantesimo di secondo il pistone accelera due volte e decelera altre due, perché in appena un centesimo di secondo deve arrivare dal punto morto superiore al punto morto inferiore, dove si ferma e riparte in senso inverso per un altro centesimo di secondo….. e così via. E’ vero che il peso del pistone, generalmente in alluminio, dell’occhio di biella e dello spinotto non sono in genere molto elevati, ma potete immaginare quale sia il martellamento e la vibrazione sussultoria indotta nella struttura.
Per ogni giro del pistone esistono due inerzie che si sommano
a) L’inerzia più importante, che deriva dall’inversione di moto del pistone al punto morto superiore ed inferiore, e che quindi agisce due volte per ogni giro
b) L’inerzia, che in fisica si definisce “di secondo ordine”, che agisce quattro volte per ogni giro, e deriva dalle accelerazioni e dalle decelerazioni che il pistone subisce quando:
1) accelera dal punto morto inferiore a mezza corsa,
2) decelera da mezza corsa al punto morto superiore,
3) riaccelera dal punto morto superiore fino a mezza corsa e
4) decelera da mezza corsa fino al punto morto inferiore.
Questa è la inerzia più noiosa, perché come vedremo, è la più difficile da compensare.
Per un motore monocilindrico non c’è rimedio: non esiste infatti la possibilità di equilibrare un moto alternativo, se non con un altro moto alternativo uguale ed opposto. Se i cilindri sono due cilindri con le manovelle a 180° ogni colpo verso l’alto è compensato da un colpo simmetrico verso il basso: le due inerzie, di uguale intensità, si annullano e così il sussulto si quieta; quello che invece non si acquieta per niente è lo scuotimento del secondo ordine, che raddoppia perché invece di due accelerazioni per ogni corsa ci si ritroverà con quattro accelerazioni (due per ogni pistone) che non possono essere compensate. L’unico modo per compensare forze in quadratura (corrispondenti cioè ad una posizione della manovella a 90° dai punti morti) è quello di distribuire la loro azione su un angolo diverso da 180°, e questo si può ottenere con un tre cilindri con le tre manovelle disposte in maniera simmetrica nei 360°, cioè angolate tra loro di 120°, che rappresenta la condizione per l’annullamento della forza risultante di entrambi i tipi di inerzia che agiscono sui pistoni
A questo punto sembrerebbe tutto a posto, ma….
Ma occorre tenere conto che per annullare l’azione delle inerzie occorrerebbe che le due, o le tre, manovelle ruotassero nello stesso piano verticale perpendicolare all’asse motore, e questo non è evidentemente possibile, perché tra una manovella e l’altra ci deve essere lo spazio per i supporti di banco e comunque la distanza che c’è tra gli assi dei rispettivi cilindri. Che succede allora? Che le forze si compensano perché sono uguali, ma siccome agiscono su assi paralleli generano una coppia che produce un beccheggio del motore, cioè una oscillazione in su o in giù attorno al baricentro, che tende ad abbassare la parte anteriore ed alzare quella posteriore e viceversa, tante volte quanti sono i giri del motore.
Per evitare questo “beccheggio” è necessario che le forze parallele che agiscono lungo l’asse dei cilindri abbiano ognuna una forza equivalente che agisce nello stesso senso dall’altra parte del baricentro in modo speculare.
Da un due cilindri nasce allora un quattro cilindri, due a destra e due speculari a sinistra del baricentro dinamico segnato in rosso nella figura
Nel quattro cilindri è vero che si sono eliminate le coppie delle inerzie primarie, ma si è ancora aggravata la incidenza delle inerzie secondarie che, da due, per ogni corsa del monocilindrico sono diventate otto per ogni corsa, si sono cioè quadruplicate, e non c’è verso di compensarle se le manovelle sono tutte a 180° tra di loro.
Se invece raddoppiamo un tre cilindri, dove già tutte le forze di inerzia sono equilibrate, dobbiamo solo occuparci di bilanciare le coppie attorno al baricentro, il che è facilmente ottenibile con una configurazione delle manovelle speculare rispetto al baricentro.
Un motore a sei cilindri in linea con manovelle distribuite a 120° simmetricamente rispetto al baricentro è dunque un motore ideale perché riesce a bilanciare tutte le inerzie e ad avere un funzionamento morbido e scorrevole, senza vibrazioni. Tanto da poter funzionare anche senza volano perché non ha punti morti da superare; questa configurazione, oltre che nei motori diesel e benzina, è stata adottata in un motore fuoribordo di ultima generazione: la scelta dei progettisti della Mercury, che nel caso del Verado hanno disegnato l’intero motore attorno ad una testa a sei cilindri in linea, è indicativa della sua perfetta equilibratura. Questioni di ingombro hanno invece indotto gli altri costruttori di fuoribordo ad optare per configurazioni a V, con alcuni vantaggi ed alcuni svantaggi, che saranno esaminati in altra occasione.
Alfredo Gennaro